
PRODUCT DEVELOPMENT.
Creating a new product is exciting and challenging. Whether you are building a bicycle frame or component, we provide support for design implementation, engineering, prototyping, testing, and tooling. We take your sketches and transform them into the end product.
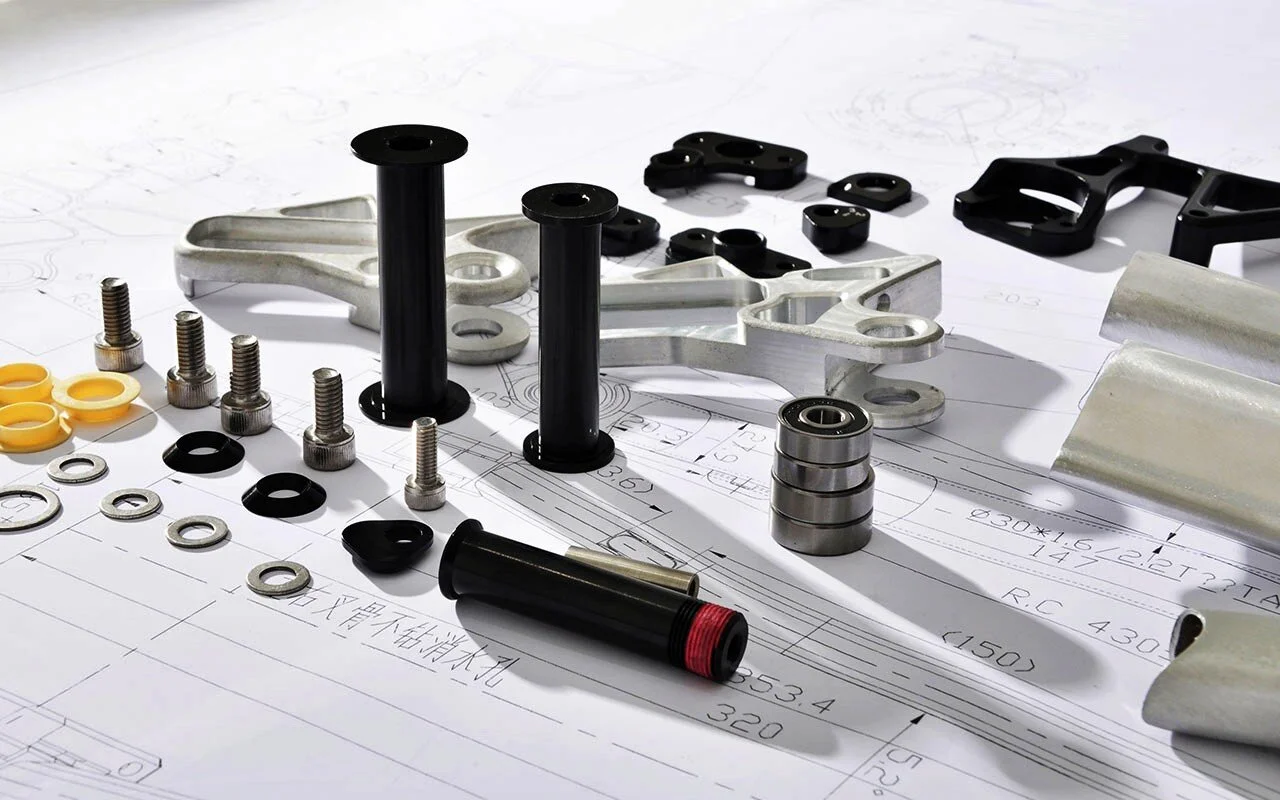
Design and Engineering.
Implementing product design and engineering for bike frames and components requires extensive communications with vendors and sub-vendors. Creating a feasible product from scratch is no simple task. Creating a product with exemplary design and sound engineering is of course dependent upon the core competencies of bike brands, but also every supplier involved in implementation so that manufacturing at scale is possible. Oerus has extensive experience working with experienced brands as well as startups realize their ideas. We create scale and 3D drawings, apply technical know-how, and build specifications.
-
We push for concept realization and can provide the initial architecture, design, and engineering for various applications. Manufacturing feasibility and adherence to cost management is key.
-
We build the 2D scale drawings and 3D renderings for various applications, including bicycle and e-bike frames, e-bike motor cages and battery systems, components, and associated hardware.
-
We work with some of the finest hardware engineers from the IT sector in Taiwan to ensure that our client applications and products are developed in tune with the functional quality required.
-
Our in-house engineers have decades of experience building steel, alloy, and carbon fiber applications, notably for bicycle frames and components, electric bike motor mounts and battery housing, motorcycle parts, drone parts, and various components.
-
We can build the Bill of Materials from start to finish, choosing the most cost-efficient and quality-driven components from our vetted network of suppliers in Taiwan, China, and Southeast Asia.
-
Development can be costly upfront. We help plan the initial product design and engineering costs in respect to time to market. We strive to optimize our client’s cost-efficiency for each project.
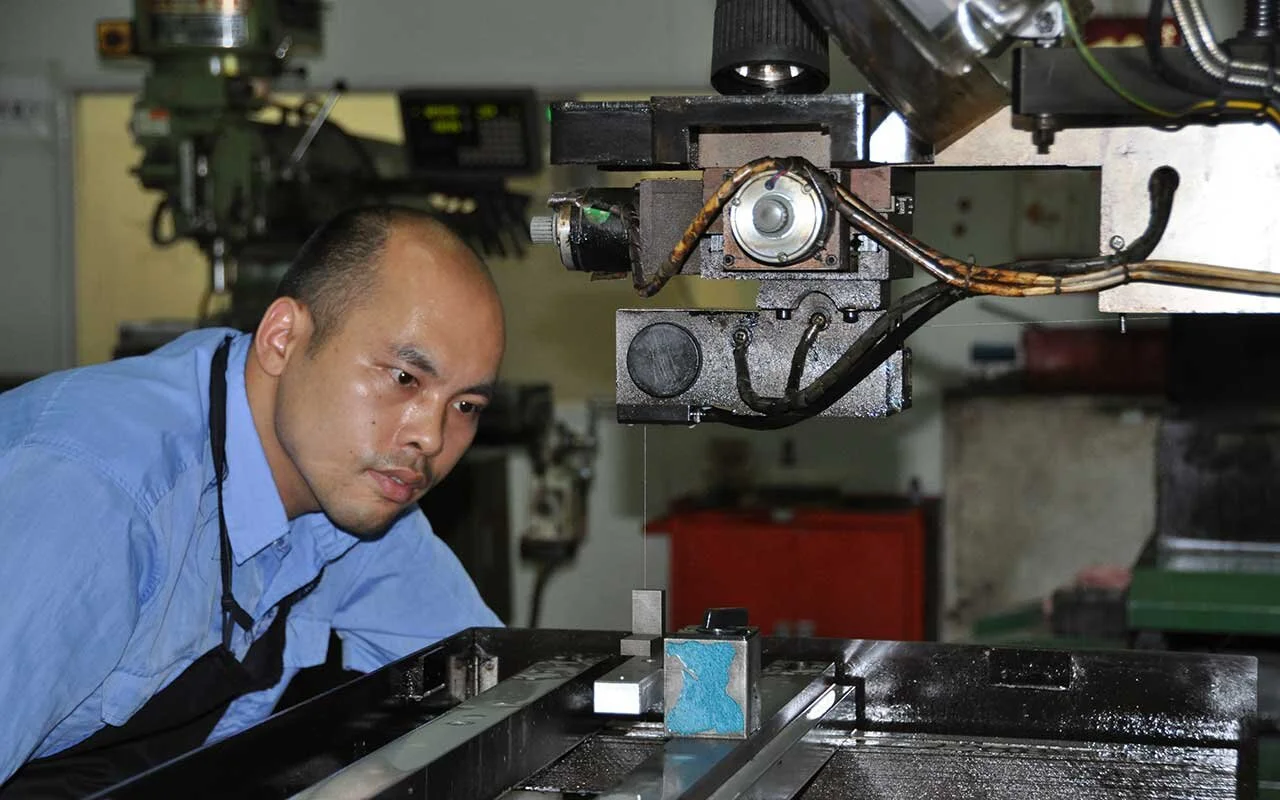
Prototyping.
Building product samples for testing and visualization is essential for perfecting product development. When samples are created, Oerus provides clients with on-site inspection services, ensuring that all design and engineering details have been achieved before they are dispatched for further utilization. Our services save clients an immense amount of valuable lead time, which contributes to overall product development efficiency.

Product Testing.
There are a plethora of testing standards and procedures for bicycles and bike components from various institutions around the world. Depending on our client’s sales distribution network regarding where products are shipped to, Oerus arranges for the necessary product testing services by third party specialists and ensures that all testing results are achieved before final production commences. We also handle all subsequent product testing certificates and due diligence to facilitate logistics and customs clearance when necessary.
-
We utilize accredited third party testing specialists to conduct testing on complete bicycles for each jurisdiction requirements.
ISO
EN
CPSC
GB
AS/NZS
JIS
ABNT NBR
ANSI
-
Compliance for USA Class 1, 2, 3.
Compliance for Europe (EN/ISO).
Compliance for Europe (L1e-B 45km/h).
Compliance for Australia (ASNZS/EN).
-
We contract accredited third party testing agencies to perform testing on bicycle and e-bike frames primarily for compliance with international standards, but also determining the limits of product safety and integrity.
Fatigue testing.
Impact testing.
Hardness testing.
Stiffness testing.
Material analysis.
Chemical analysis.
Paint testing.
-
Like frames, we also contract accredited third party testing agencies to perform testing on bicycle and e-bike components for compliance with international standards, but also determining the limits of product safety and integrity.
Fatigue testing.
Impact testing.
Static strength testing.
Torsional strength testing.
Brake testing (Wet and Dry).
Hardness testing.
Stiffness testing.
Material analysis.
Chemical analysis.
Paint testing.
-

Tooling.
When creating a custom bike frame or component, tooling is designed and built for the purpose of minimizing mass production costs. There are many different types of tooling systems utilized in the bicycle and e-bike manufacturing industry which are also used for motorcycles, automotive, and aerospace industries. There are significant upfront costs when creating such tooling systems and the molds created are considerable investments that require proper due diligence for protection of intellectual property and maintenance for prolonged usage. Oerus utilizes a variety of widely available tooling methods when helping clients develop new products.
-
Hot forging of alloy and steel is used to create a variety of parts for the purpose of mass production. Applications include bicycle frame parts such as dropouts, rockers, gussets, as well as bicycle components such as shocks, levers, cranks, stems, and pedals.
-
Like hot forging, cold forging to create the tooling for mass production of a variety of applications ranging from bicycle and motorcycle parts.
-
A procedure commonly used to produce custom design alloy hydroformed tubing used for bicycle frames, automotive, aerospace, and medical device applications.
-
Die casting is a procedure typically used for creating the tooling for frame parts, bicycle stems, bicycle seat posts, bike pedals, e-bike motor cages and housings, and many motorcycle parts.
-
Gravity die casting is used to create more complex applications for E-bikes (frame parts, motor housings, and hub shells), Motorcycles (frames, swing arms, cylinders, gearbox housings).
-
The procedure used for developing the tooling used to produce thermoplastics and polycarbonate applications for Bicycles and E-bikes (grips, protectors, cable guides, saddles, and insulator parts).